GUD Filters
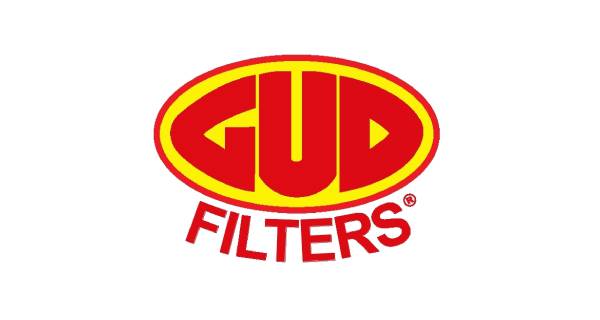
REVIEWS
PHOTO GALLERY
ABOUT US
The leaders in advanced engine protection
GUD Filters, South Africa's leading automotive filter brand manufactured its first filter in Durban in 1949. As the automotive industry evolved so the Company expanded over time to become the market leader in South Africa.
G.U.D. Filters has manufacturing facilities in Pietermaritzburg, Durban, Cape Town and Zimbabwe. GUD also has a distribution centre in Pinetown, geared towards our export market, and a 20 000m2 distribution centre in Johannesburg. The company's headquarters is in Prospecton, KwaZulu Natal and it employs in excess of 1500 people.
GUD Filters has extended its success across international boundaries and currently exports to five continents. GUD places great emphasis on quality to exceed the requirements of all its market.
Quality
The GUD Filters quality system is regularly assessed by the South African Bureau of Standards to TS 16949: 2009. Our quality system, products and processes are audited regularly by OEMs to ensure their specific requirements are met and to this end, we have achieved the coveted Ford Q1 Status.
Our dedication to quality and customer satisfaction cultivates a team ethic that extends throughout the company, and includes suppliers of raw materials and services. A supplier development program encompassing quality, productivity and costing issues is vigorously pursued.
The effectiveness of the entire GUD quality system and its quality ethic has been a cornerstone of the company since its inception; thereby ensuring products consistently perform to the highest standards.
SERVICES
Diesel Fuel Filters (Multiport)
GUD celebrated one of the most exciting manufacturing developments in the company's history, with the opening of our diesel filter line. The line boasts technology and performance standards unparalleled anywhere in the industry.
The line operates in a clean room environment comparable to the operating room of a hospital. Diesel filters operate under extremely high pressures, and as a result, there is a huge danger of dirt damaging the injectors. For that reason, the clean room was designed to minimise the build-up of dirt in the actual manufacturing process, almost completely eradicating any impurities up until the time of the filter being installed in the vehicle.
With all doors air-locked, all joints fully sealed, and air conditioning entering through eight dual filter packs to create an over-pressured enclosure, the manufacturing environment is impeccably clean, comfortable, and secure from outside contamination. In addition to this, employees operating on the line do so wearing specially designed lint-free suits.
The focus on hygiene is continued throughout the packaging and inspection process, to ensure that no dirt can accumulate along the way. All components are cleaned internally and stored in appropriate containers and racks. Furthermore, received goods are suitably protected to ensure the continuation of the cleanline standards.
The smaller size of diesel engines, as well as the higher speed at which they function, creates a need for decreased tolerances and therefore maximum efficiency in order to ensure Extended Service Intervals. GUD products are guaranteed to meet and exceed the efficiency needs of a modern diesel engine. These filters feature highly complex piping (hence the name, multiport), which serves to perform the following functions:
- Inlet from tank.
- Outlet to engine.
- Excess fuel back to sump.
- Hot fuel back from injectors to warm the diesel to prevent the wax in diesel solidifying at colder temperatures.
- A water extractor point. If there is no pre-filter, water will be removed by the multi-layer media and have to be sucked out by a special device.
Rigorous testing and research went into the design of the room and equipment, and it serves as testimony to GUD’s unwavering commitment to going beyond market expectations to provide customers with the highest quality products possible. GUD’s sterile manufacturing room and rigid controls give us a distinct competitive advantage as we strive to go the extra mile to ensure your car’s engine can do the same.
GUD vs. Competitor
The purpose of a filter in your engine is to KEEP OUT HARMFUL CONTAMINANTS, carried by the engine’s air, oil and fuel supplies.
Contaminants can be in the form of dust, sand, soot, water and engine wearing metals. If these contaminants are NOT filtered out, rapid engine wear will occur or worse, COMPLETE ENGINE FAILURE.
A sub-standard filter WILL result in premature wear. On the face of it and to the untrained eye, sub-standard filters often don't look bad from the outside and are therefore deemed to be good quality. This is where the unsuspecting are led astray. Filtration performance far outweighs physical appearance.
To ensure you fit the best quality filter to your vehicle, follow these simple rules and be assured of Great Engine Protection and maximum engine life:
- Always buy a reputable and trusted brand, such as a GUD Filter.
- Always look for a comprehensive product warranty, as offered by GUD
- Filters; as opposed to a warranty that will replace only the filter and not cover the damage done to the vehicles' engine.
- Always ensure that the brand you fit to your vehicle meets or exceeds the original equipment vehicle specification, as GUD Filters do.
FACT:
South African conditions may require shorter oil service intervals than those in Europe and the East. This is because of our higher dust concentration, extreme changes in altitude, our vehicles’ higher working loads and poor fuel quality.
Proudly South African
G.U.D. Filters is a proudly South African brand that is committed to supporting local suppliers and local sources of raw materials since 2002. We further support South Africa's economy through employment opportunities and adhering to fair labour practices.
In 2013 G.U.D. was honoured with the Proudly South African Enterprise award at the Inaugural SA Premier Business Awards. The Proudly South African Enterprise Award recognises the contribution that G.U.D. Holdings has made toward high quality local products and for being a proud and active member of the Proudly South African Campaign.
G.U.D. has also won several South African Home Grown awards over the years which attest to our efforts in supporting the campaign.
- 2004 - Product of the Year
- 2005 - Exporter of the Year
- 2006 - Exporter of the Year
- 2006 - Company of the Year
- 2007 - Manufacturer of the Year
- 2007 - Product of the Year
Community Upliftment
G.U.D. Filters is a socially responsible brand. We recognise the importance of a good education and highlight this by uplifting learners and education facilities in our community.
Over the years we have invested substantially in the education of learners from Zenzele Primary and Christel House South Africa among others in the form of bursaries and financial assistance for the operations of these schools. Our dedication to empowering disadvantaged students is also extended to physically challenged students from Fulton School for the Deaf and the Open Air School.
We also place a key focus on youth development through sport and support this belief by being the largest player sponsor of the Sharks Academy, a training school accredited by SA Rugby based in Durban.
It is our mission to be a socially responsive organisation that is committed to improving the lives of our employees and their families, the communities that surround us and our country. We accomplish this through the great engine protection and reliability our filters offer to motorists.
The practice of environmental responsibility at GUD
GUD adopts a strict Occupational Health, Safety and Environmental policy and for this reason we were awarded the internationally recognized ISO14001:2004 environmental management system compliancy certificate. Key elements of these policies and procedures are the prevention of pollution, the preservation of natural resources, the management and minimization of waste, compliance with applicable environmental legislation and a process of continual improvement in environmental practices.
GUD has also received ISO 14001:2004 accreditation for Environmental Management Systems, with all our manufacturing sites conforming to the standards of the system. GUD firmly believes in taking the utmost care in looking after our environment, and the ISO 14001 accreditation is testament to this; pertaining to all activities, practices and services controlled or influenced by the company. The benefits have been immense and have taught personnel the value of recycling and preventing pollution in any way, shape or form.
Marketing
As brand leaders, GUD Filters promises motorists great engine protection and sets the pace and standards in the industry when it comes to innovative and outstanding value-added marketing practices.
Our GUD Auto Detox programme which was launched in 2009, offers motorists a quick valued added oil and filter change between regular vehicle services to prolong engine life on todays congested roads. The GUD AUTO DETOX programme has grown from strength to strength over the years and has a dedicated website, www.gudautodetox.co.za to direct motorists to Workshops that offer GUD AUTO DETOX.
GUD also has a long established Winning Partnership Program, partnering with independent workshops around the country. The company has established strong relationships with motor spare retailers and OE vehicle manufacturers.
GUD Product Warranty
- In the event that any GUD Filter (“Filter”) is unsuitable for its intended purpose, of poor quality, not in good working order, defective, substandard or fails during the service life of the Filter, G.U.D. Holdings (Pty) Ltd (“GUD”) will, subject to the limitations explained below:
- replace the Filter; or
- refund the price of the Filter.
For the purpose of this warranty “Service Life” shall mean the Service Interval specified by the vehicle manufacturer for the specific vehicle to which the filter was fitted.
- Notwithstanding the above, if any physical harm to person or property is caused as a consequence of:-
- GUD supplying unsafe Filters;
- a failure, defect or hazard in any Filter.
As set out in the Consumer Protection Act, GUD will, to the extent liable in law and on the facts, pay for loss/damages resulting from that harm.
GUD’s obligations in terms of this paragraph will be limited to the duration of the Service Life of the Filter unless the Consumer Protection Act requires otherwise.
- In order to obtain the remedies set out above, the purchaser of the Filter must make use of GUD’s claims procedure, available on request by email to marketing@gud.co.za or at www.gud.co.za.
- GUD will have the right not to provide the remedies set out above to the extent that the Consumer Protection Act does not oblige GUD to do so in the circumstances of a particular case.
- Counterfeits: GUD will not be liable for any damages arising from fitting counterfeit filters.
GUD Claims Procedure
The following procedure must be followed in respect of claims arising from any defect, malfunction, failure or hazardous characteristic of a Filter sold by G.U.D. Holdings (Pty) Ltd (“the Company”) and must be read with the applicable Product Warranty.
- The Claimant must complete the claim form, available from marketing@gud.co.za or www.gud.co.za
- If it appears that any person or property has been harmed or damaged because of the defect, malfunction, failure or hazardous characteristic of the filter, all documents which show the extent and cost of the harm or damage (such as quotations or invoices for repair services) must be attached to the claim form. Information about steps that may have been taken to stop or limit any damage resulting from the defect, malfunction, failure or hazardous characteristic of the filter must also be provided.
- If it is alleged that damage has been caused to an engine, the Company must be given immediate access to the engine.
- The filter must be returned to the Company together with the claim form and supporting documents.
- The above steps must be done within 30 days of the Claimant becoming aware of the defect, malfunction, failure or hazardous characteristic.
- Once the filter has been returned to the Company a representative of the Company will inspect the filter in order to determine whether the filter is in fact defective or hazardous or has in fact malfunctioned or failed and if so, whether the defect, malfunction, failure or hazardous characteristic caused harm to a person or damage to property.
- Once the filter, claim form and supporting documents have been inspected, the Company will determine whether in fact the filter is defective or hazardous or has in fact malfunctioned or failed and if so, will offer to remedy the defect, malfunction or failure and, where applicable, harm suffered by way of the various options available.
- These options could include, for example, the replacement or repair of the filter and will always include remedies given to consumers under the Consumer Protection Act where these remedies are applicable to the facts of the case and where the time for such remedies set out in the Consumer Protection Act, has not run out.
- In the event that the conclusion of the representative of the Company is disputed, the Claimant may appoint an independent person (at his cost) to assess the claim. If this is done and the independent assessor comes to a conclusion different to that of the Company representative, the Company representative will re-consider his conclusion and advise whether or not the original conclusion is changed.
- Claimants will always be entitled to pursue claims in respect of sub-standard, unfit, failed, hazardous, unsafe or defective filters as contemplated in the Consumer Protection Act, using the specific mechanisms set out in chapter 3 of the Consumer Protection Act.
- In order to finalise any resolution or settlement of a claim relating to a defect, malfunction, failure or hazardous characteristic and, where applicable, any resulting harm, the Claimant will be asked to sign a discharge.